Case History.
A Midwest nut and snack company reduced the number of line workers from four to one. The company was suffering from increased labor costs and decreased line yields because chocolate covered pretzels were shingling. Several line workers were needed to manually align the product downstream of the vibratory conveyor. The vibrating conveyor was shingling the pretzels due to the vertical pitching motion to propel material with repeated impacts.
Triple/S Dynamics installed a Slipstick De-shingling Conveyor. The gentle horizontal, slow-advance, quick-return motion combined with aligning lanes and special de-shingling ramps provided high de-shingling efficiency and also reduced salt loss from pretzels. The unique horizontal differential motion glides the product down the pan, eliminating breakage problems for fragile foods. The consistent conveying motion throughout the length, width, and depth of the product bed helps prevent the build-up of oily fines. And because it isn’t dependent on impact to provide motion, the Slipstick conveys deep product beds uniformly, with no stratification.
The Slipstick De-shingling Conveyor increased productivity by significantly reducing the number of shingled pretzels that resulted in scrap, therefore increased line yields and reduced labor costs.
Equipment/ People we like.
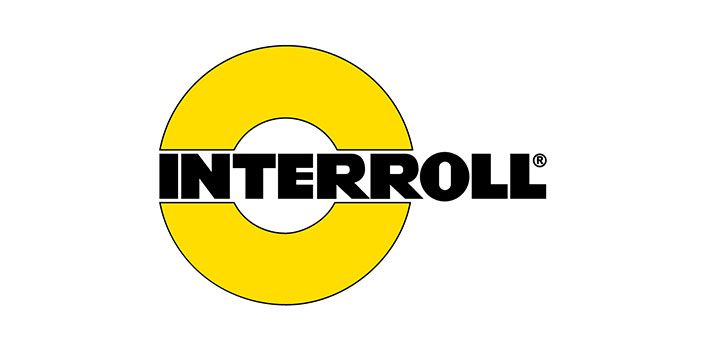
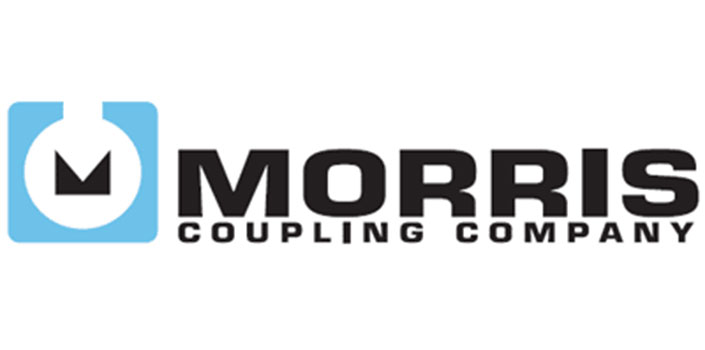
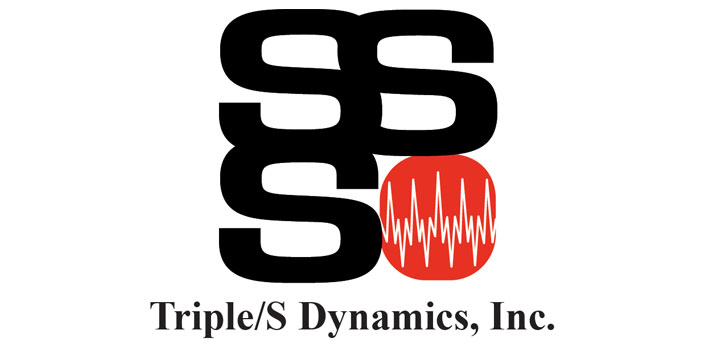
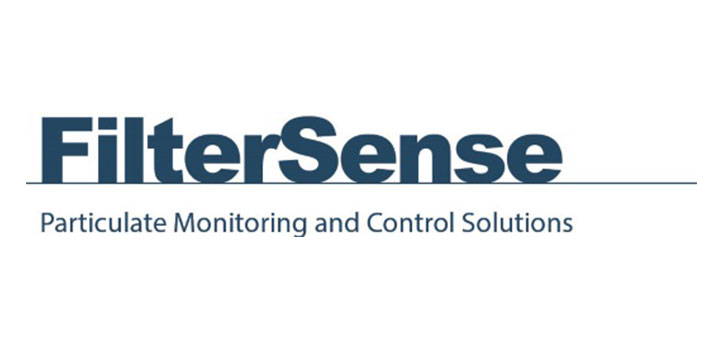
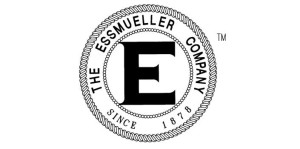
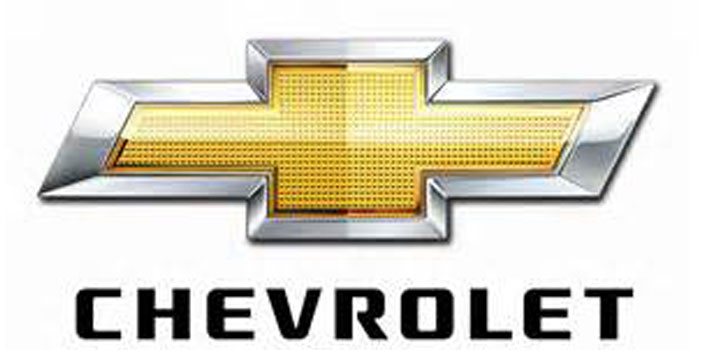
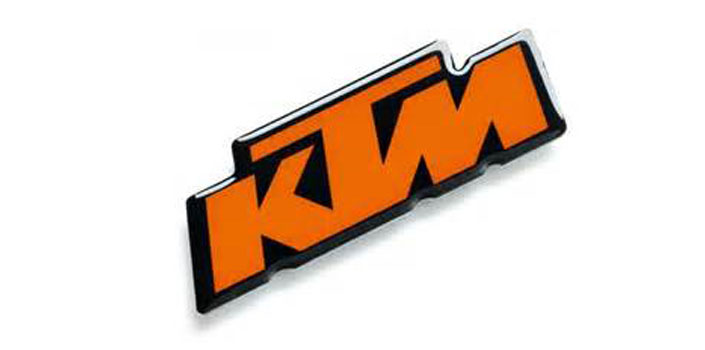
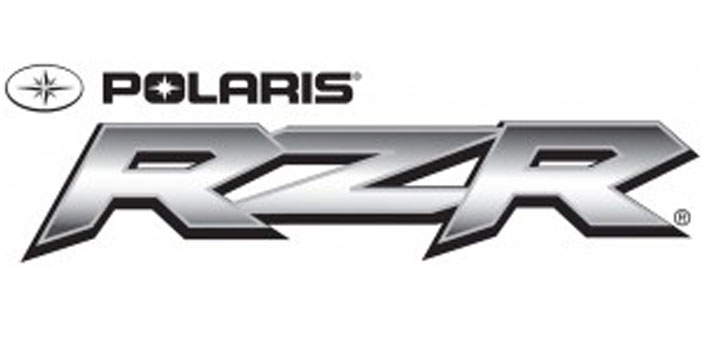